How postponing warehouse automation can cost your e-grocery business
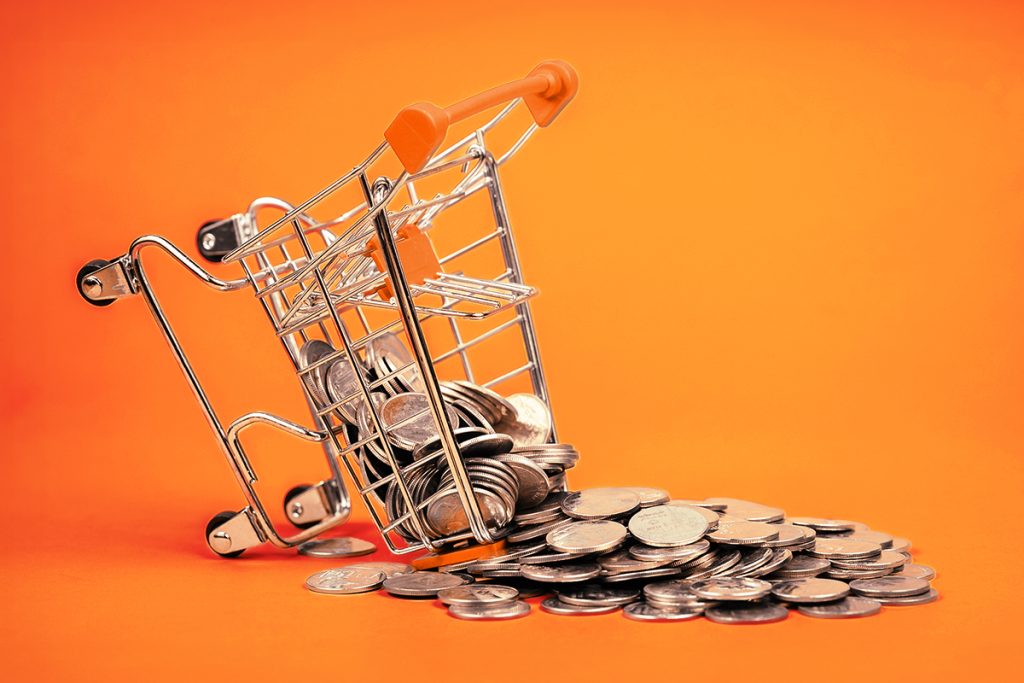
E-grocery is a cutthroat, low-margin business. To stay competitive and profitable, e-grocers need to drive efficiency and consistency across their entire supply chain. That is why warehouse automation has gone from a “nice-to-have” to a core part of many e-grocers’ strategy, with 1 in 7 grocers deploying warehouse robots in 2023.
Whether you’re Director of Innovation, VP of Operations or a C-level executive, postponing warehouse automation can affect your performance by exposing yourself to cost inflation, labor shortages and operational mistakes. Let’s explore why putting off automation could harm your e-grocery business.
Loss of customers due to escalating fulfillment costs
High inflation has made consumers increasingly price sensitive and more likely to switch to a competitor if you raise prices. This can be especially problematic for e-grocers because your competition is just one website click away and consumers can easily compare prices online.
Delaying automation means exposing your business to rising labor costs, which inevitably trickle down to consumers in the form of higher prices. In today’s challenging economic environment, this can make the difference between a sale and an abandoned cart.
Consider this:
According to a GroceryDive survey, 89% of grocers view optimizing order fulfillment as a major opportunity for cost savings.
Warehouse robots such as Brightpick Dispatcher enable grocers like Rohlik Group to significantly cut fulfillment costs and reduce labor expenses. By doing so, you are not just preserving margins but also ensuring competitive pricing for your customers and building long-term customer loyalty.
Customer dissatisfaction due to human error
Consumers buying groceries online expect fast and accurate order delivery. Human errors in the picking process can result in incorrect or delayed orders, leading to customer dissatisfaction, costly returns, and even loss of valuable customers.
Consider this:
Continuing to rely on human labor for picking can lead to a high error rate, increased refund or appeasement costs, and even damage to your brand’s reputation with customers. That is why automation is crucial for delivering best-in-class customer service and why e-grocers are installing Brightpick Autopicker robots to achieve a 10x reduction in picking errors.
Unnecessary business disruption
The warehousing industry experiences some one of the highest rates of staff turnover, averaging almost 40% per year. High staff turnover is a hidden drain on resources. It leads to:
- Costly hiring: Constantly recruiting and training new staff is expensive.
- Training expenses: Training new hires who may leave soon wastes valuable resources.
- Staff shortages: Difficulty filling positions places more pressure on existing employees.
Imagine being unable to meet customer demand because you can’t find enough people to fulfill orders in your warehouse. Delaying automation exposes your business to these avoidable risks.
Consider this:
51% of executives believe implementing automation will increase employee satisfaction.
Brightpick offers a user-friendly solution that requires minimal training for your warehouse associates. This simplifies onboarding and hiring processes, saving you valuable time and resources. Plus, with Brightpick robots handling order picking, consolidation, and dispatch, you reduce your dependency on human labor. This ensures smooth operations that can quickly adapt to changing demands.
Scalability challenges
The ability to easily scale up or down is essential for e-grocers. Customer demand for e-groceries skyrocketed during Covid, surging by 55% in Europe during the peak of the pandemic. The sudden spike in orders demonstrated the need for e-grocers to rapidly adapt to changing customer expectations.
Manual operations, while flexible in some regards, often struggle with spikes in demand because adding labor on short notice is typically challenging and costly.
This is where warehouse automation can help. Brightpick’s robots empower e-grocers to scale on short notice without even adding additional robots or people. Here’s how:
- Advanced picking: Brightpick Dispatcher, which automate post-pick order consolidation and dispatch, enable grocers to pre-pick orders in advance and store them in a temporary buffer area until they need to be dispatched. This enables your warehouse to prepare orders during off-peak hours and thereby increase how many orders you can ship during peak hours.
- 24/7 operations: You can easily extend the operating hours of your warehouse because you no longer need to add lots of labor to do so – Brightpick robots do all the heavy lifting and require minimal labor to operate.
The inevitability of automation
Leading e-grocers are already adopting automation at scale. Delaying automation means you risk being left behind while competitors reap the benefits of enhanced efficiency, lower fulfillment costs, and improved customer satisfaction. Why postpone the decision for much longer when you can help your business today? Brightpick offers a path to fully automated fulfillment with ease!