3PL
Win and retain
more customers
Improve margins and offer superior pricing models by reducing your fulfillment costs
Brightpick offers multi-purpose AI robots for 3PLs to easily automate every step of their order fulfillment
Why 3PL companies need automation
Common challenges for 3PLs
- Low profit margins Squeezing out profits while trying to offer competitive pricing
- Expensive labor Poor availability and high cost of warehouse labor limits growth and profitability
- Lots of seasonality Need to ramp operations up and down for peak season
- Demanding customers 85% of shoppers want same-day shipping and free returns
- High error rates Picking errors reduce customer satisfaction
- Dynamic client base Client turnover and need to serve a wide variety of clients
How Brightpick helps
- Minimizes labor requirements
- Reduces fulfillment costs
- Eliminates human picking errors
- Speeds up order picking
- Boosts throughput without adding footprint
- Requires 0 fixed infrastructure
- Improves customer and employee satisfaction
of 3PLs rank automation among their top three opportunities for 2024
How it works:
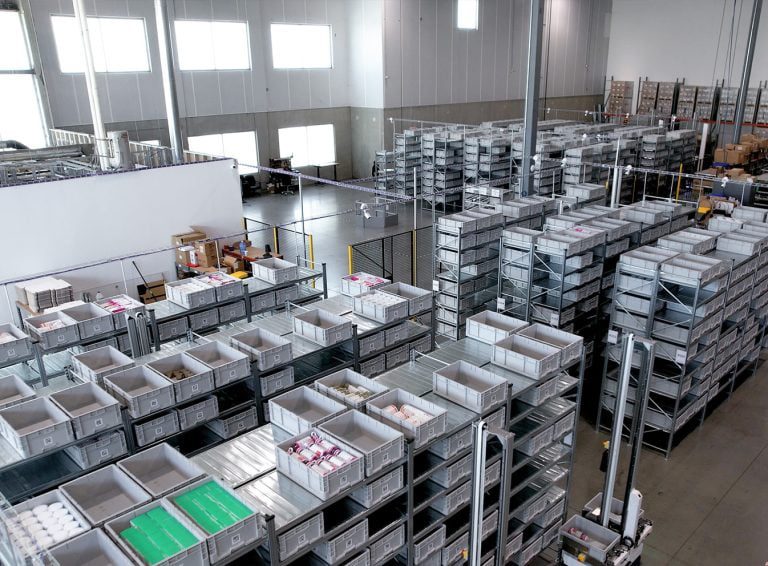
Case study
Netrush increases margins using Brightpick robots
Netrush is a US-based 3PL whose main warehouse facility in Northern Kentucky ships out 20,000 orders per day.
The company wanted to automate their order picking and replenishment to reduce costs, streamline operations and increase competitiveness. They needed a solution that was easy to scale, so they could start with a few robots and expand it on-demand as they added new customers into the system.
With Brightpick, Netrush was able to:
- Fully automate picking and putaway without any major changes to their existing processes and facility
- Reduce labor for picking and replenishment by over 75%
- Eliminate bottlenecks in picking
- Double storage density by using narrower aisles and taller shelves
“ We saw almost a 4x increase in picking and packing thanks to Brightpick. This unlocked a lot of opportunities for our customers. We’re now able to offer kitting and bundling that were previously too labor intensive for us. All this translates into happier customers and, of course, lower costs. ”
Brian Birch
Chief Supply Chain Officer, Netrush
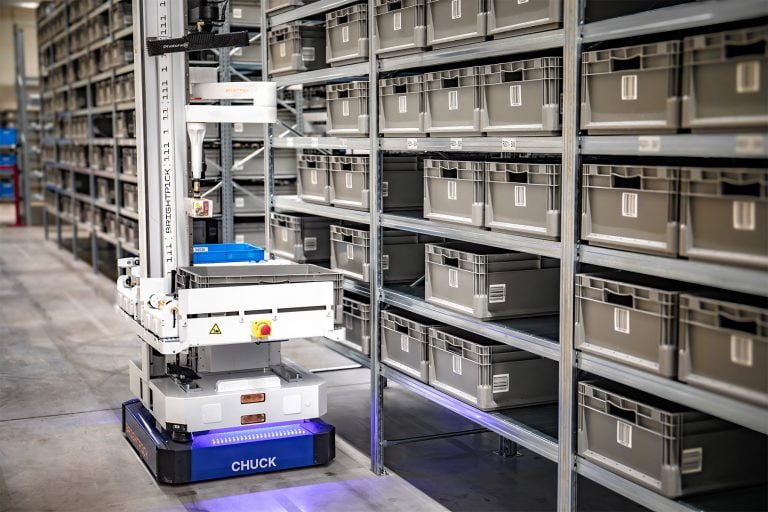
Maximum Flexibility
Brightpick ensures 3PLs retain full flexibility even with end-to-end automation
Say goodbye to conveyors, safety fencing, special sprinkler systems and fixed navigation markers.
All you need to fully automate your fulfillment is standard shelving and totes. You can even move our robots and shelving from one warehouse to another.
Impact
How will Brightpick
make my job easier?
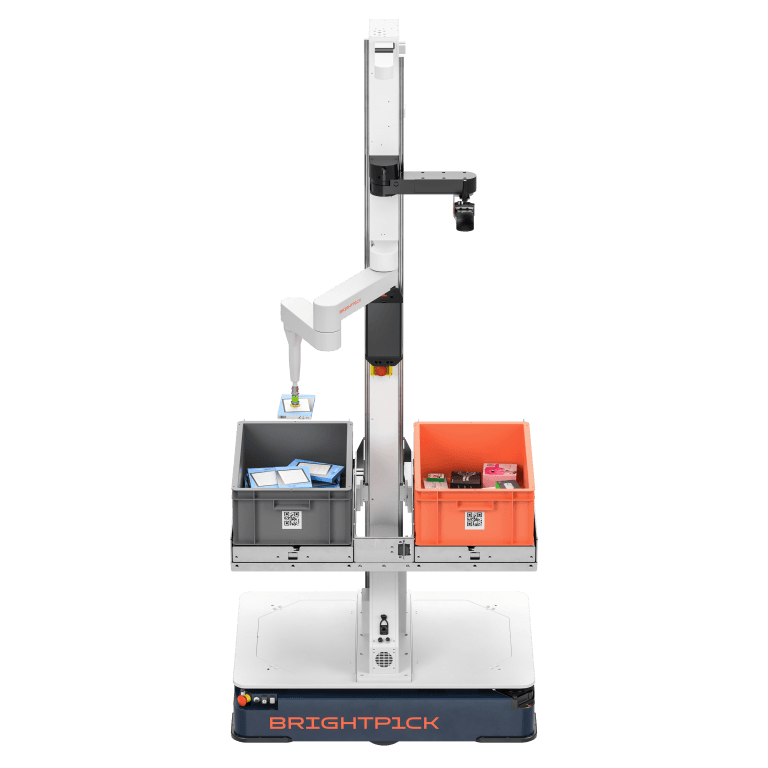
ROI
Fast payback, immediate results
Achieve payback in as little as one year with Brightpick.
By minimizing labor needs and eliminating human errors, you can significantly cut costs and boost margins while improving fulfillment speed, customer satisfaction, and operational efficiency.
Explore the ROI potential for your business.
Pricing and ROIImprove profitability and offer better pricing models by reducing your fulfillment costs.
Improve customer satisfaction and reduce returns by eliminating human picking errors.
Store more inventory and fulfill more orders from the same warehouse footprint.
Minimize upfront costs and maintain flexibility to move or reconfigure the automation as needed.
Speed up order picking and always meet your SLAs without adding footprint or labor.
Reduce supply chain risk and achieve 99.9% uptime with no single point of failure.
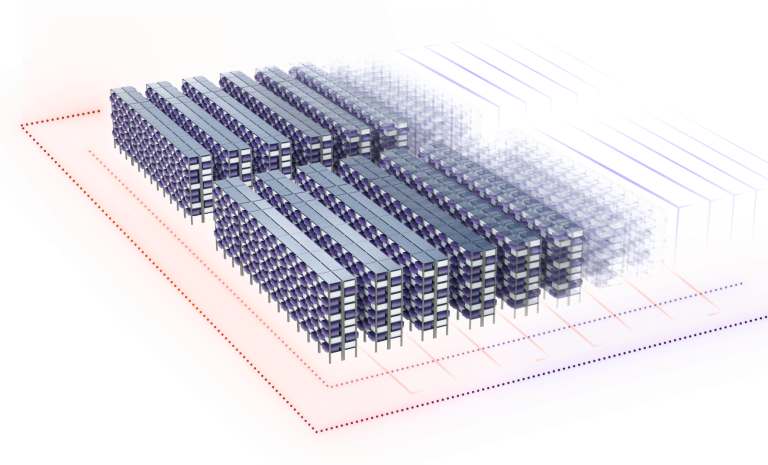