Medical
Take the risk out of medical fulfillment
Enhance order accuracy, reduce labor costs, and effortlessly meet regulatory requirements
Brightpick offers multi-purpose AI robots for medical distributors to easily automate every step of their order fulfillment
Why PHARMA and medical distributors need automation
Common challenges for distributors
- Cost inflation Rising costs and poor labor availability hurts profitability and growth
- Increased demand for LUM / piece picking Requires more labor and increases risk of errors
- High risks from picking errors Errors in pharmaceutical orders can have life-or-death consequences
- Strict SLAs and short fulfillment windows Short timelines require rapid order fulfillment without compromising on accuracy
- Need for order consolidation Large orders require efficient consolidation and sorting before dispatch
- Regulation Evolving and strict regulations for tracking and quality control
How Brightpick helps
- Eliminates human picking errors
- Facilitates regulatory compliance and inventory tracking
- No single point of failure
- Ensures critical orders are always shipped on time
- Minimizes labor requirements
- Speeds up order picking
- Increases customer and employee satisfaction
of warehouse operators already use or plan to start using robots within the next 3 years
How it works:
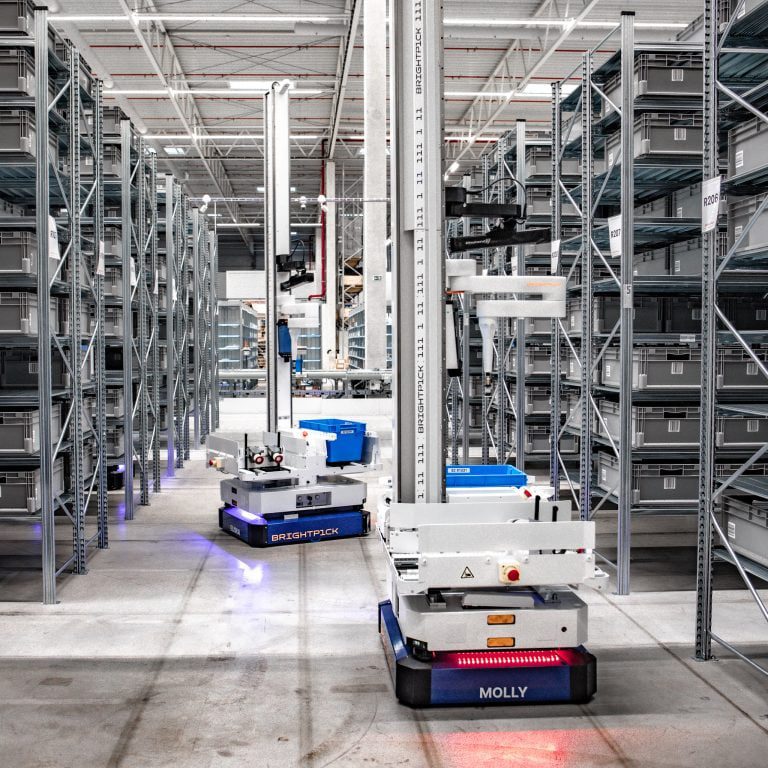
Case study
European pharmacy giant Dr. Max automates order picking with Brightpick Autopicker
Dr. Max is the second largest pharmacy chain in Europe with 3,000 pharmacies across 6 countries. The company uses Brightpick Autopicker robots to pick and consolidate orders to regularly replenish pharmacies and hospitals.
The company faced several challenges in its previous order picking and replenishment processes, including high labor intensity, picking errors and limited scalability
With Brightpick, Dr. Max was able to:
- Reduce labor for picking and putaway by 100%
- Increase throughput by 40% from the same footprint
- Eliminate human picking errors and improve order accuracy
- Enhance scalability to meet future growth needs
“ Brightpick enabled us to reallocate all our human pickers to quality control instead. We also see that the picking error rate has improved. ”
Tomas Seget
Deputy Director of Logistics at Dr. Max
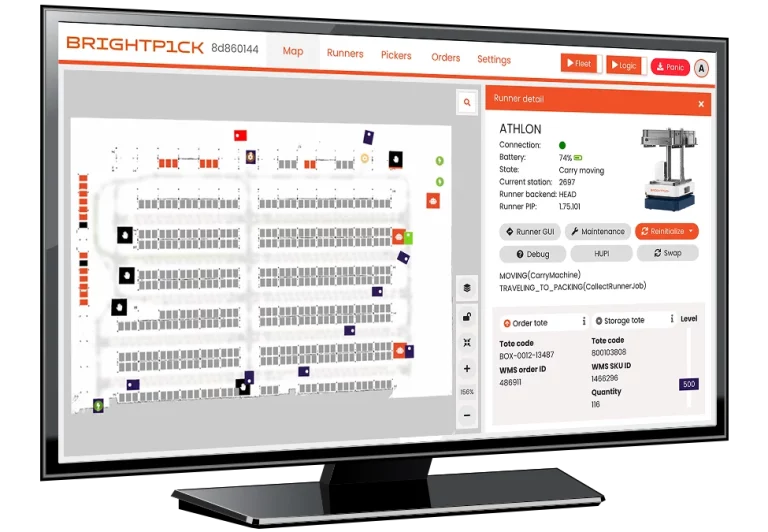
Boost inventory accuracy
Improve inventory visibility and tracking
Our software tracks each SKU and batch independently and can quickly isolate and recall a specific batch when needed.
You can also implement custom picking strategies, such as First-Expiry-First-Out (FEFO), FIFO, or LIFO, to optimize inventory management.
In case of emergencies, like power outages or natural disasters, manual access to all inventory remains unobstructed, ensuring business continuity.
Impact
How will Brightpick
make my job easier?
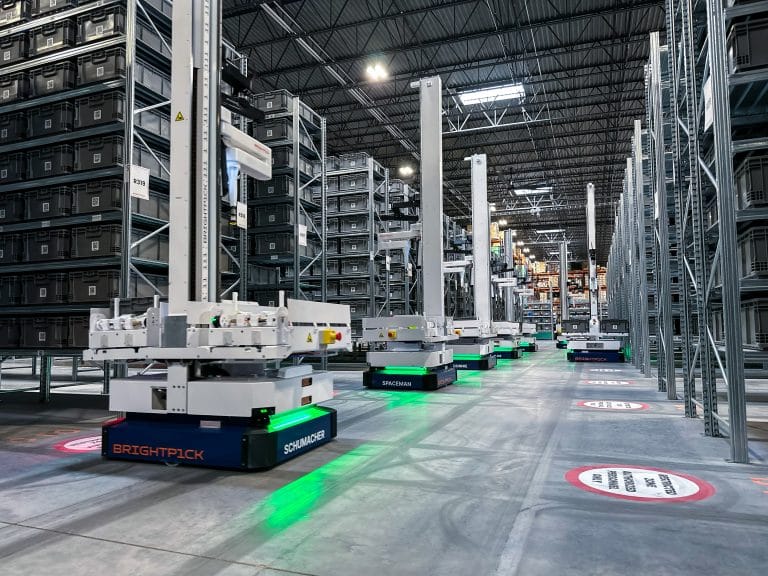
Pricing
Flexible pricing models
Brightpick is available through Robots-as-a-Service (RaaS), starting from just $1,900 per robot / per month.
RaaS transforms warehouse automation from a large upfront capital investment into a manageable monthly operating cost, which reduces financial risk, simplifies budgeting, and delivers immediate ROI.
Alternatively, the Brightpick solution is also available through a standard CapEx purchase.
Learn moreImprove profitability and offer customers better prices by reducing your fulfillment costs.
Improve customer satisfaction and reduce returns by eliminating human picking errors.
Store more inventory and fulfill more orders from the same warehouse footprint.
Minimize upfront costs and scale throughput gradually based on your needs.
Speed up order picking and fulfill more orders without adding footprint or labor.
Reduce supply chain risk and achieve 99.9% uptime with no single point of failure.
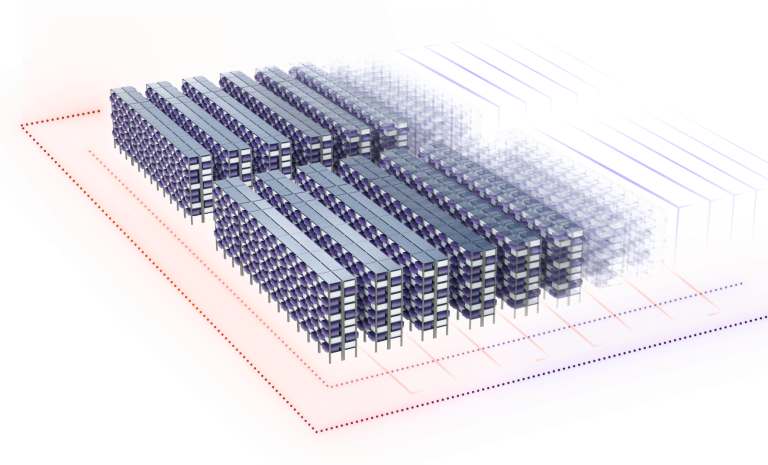