Frequently Asked Questions
General
-
What is Brightpick?
Brightpick is a leader in AI-powered robotic solutions for warehouses. The company’s multi-purpose AI robots enable warehouses of any size to fully automate order picking, buffering, consolidation, dispatch, and stock replenishment. The award-winning Brightpick solution takes just weeks to deploy and allows companies to keep their warehouse labor to a minimum.
-
Where is Brightpick based?
Brightpick is headquartered near Cincinnati, OH. We also have an Innovation Hub in Bratislava, Slovakia, where we do all our R&D and manufacturing.
-
When was Brightpick founded?
Brightpick was founded in 2021.
-
How big is Brightpick as a company?
Brightpick has over 250 employees across our U.S. and European offices. We have deployed hundreds of robots with customers and have secured approximately $100 million in funding to date.
Pricing and ROI
-
How much does Brightpick cost?
Brightpick offers both traditional CapEx and Robots-as-a-Service (RaaS) purchase options. Each solution is designed to your specific needs and throughput requirements, so pricing will depend on your specifications. RaaS pricing starts at US$1,900 per robot per month in the U.S. for a minimum three-year commitment, with additional discounts for longer-term agreements.
You can see more detail on our pricing and the expected ROI you can achieve here.
-
What is the ROI / payback period?
Companies opting for a CapEx purchase typically recoup their investment in Brightpick within 1-3 years, while those on a RaaS subscription often see payback in under six months. Actual ROI will depend on factors such as shifts per day, labor rates, and baseline manual productivity. ROI benchmarks from our customer installations are available here.
-
What sort of cost savings can I achieve with Brightpick?
Under a CapEx purchase model, Brightpick typically reduces labor costs for fulfillment and inventory management by 70-90%. Under a RaaS subscription, Brightpick delivers savings of 40-70% after accounting for the monthly RaaS fee. Actual results vary based on shifts per day, labor rates, and baseline manual productivity.
-
How much labor can I save with Brightpick?
With Brightpick, warehouses can cut fulfillment and replenishment labor by 70–90% versus manual operations. Actual savings depend on your current pick rates and the share of SKUs suited for robotic picking.
-
Can I buy a single robot?
We provide a complete solution rather than individual robots, including software, installation, and support. Our smallest deployment starts at 8 robots.
-
Do you have a pilot program?
We are always happy to discuss a pilot project, however it needs to be tied to a larger project down the line. The pricing will depend on the size of the application.
Robots
-
How do the robots navigate?
Brightpick robots use SLAM (Simultaneous Localization and Mapping) and AI-based navigation, relying on LiDARs and 3D vision to sense and map their surroundings. They do not require floor-mounted QR codes, magnetic tape, or other fixed infrastructure.
-
What type of items can Brightpick Autopicker pick?
Autopicker can reliably pick a wide range of items right out of the box without any custom training. Powered by advanced 3D vision and AI, it handles everything from medical devices to chilled groceries, polybagged apparel, electronics, cosmetics, supplements, pharmaceuticals and more.
Trained on over a billion picks to date, the Brightpick robot fleet continues to learn from every pick, continuously improving accuracy and reliability. In addition, each robot also has Goods-to-Person capabilities for complex and heavy items, batch picks, and as a fallback to robotic picking
-
What is the maximum weight per pick?
Autopicker can pick items weighing up to 5.5 lbs (2.5 kg); the robots automatically take heavier items to a Goods-to-Person station for picking.
-
What is the smallest pickable item?
Autopicker can pick items as small as 0.8” (20mm) in diameter.
-
Can Brightpick Autopicker pick multiple orders simultaneously?
Yes. Our order totes can be divided into two sub-sections for simultaneous picking of two discrete orders. Our robots can also batch multiple orders into a single tote.
-
Can Brightpick Autopicker pick orders directly into cardboard boxes?
We are developing this capability.
-
Do Brightpick robots work in chilled and frozen environments?
Brightpick robots operate reliably in refrigerated and chilled environments with stable temperature and humidity. They are not designed for frozen (sub-zero) conditions.
-
Do the robots require safety fencing?
No, the Brightpick solution does not require safety fencing. The system is designed for qualified technicians and employees to enter at any time and safely walk around the robots without pausing the system.
-
How long does the robot's battery last?
A full battery lasts 12–13 hours, with 1 hour of charging yielding 6–7 hours of work. Robots autonomously manage their charging, and our software’s smart-scheduling ensures all robots are available for work during peak hours.
-
What are the power requirements to charge the robots?
Brightpick robots charge using standard power outlets (110V in the U.S. and 220V in Europe) and do not require any special electrical power.
-
What happens if a robot breaks down?
If a robot breaks down, other Brightpick robots and workflows remain unaffected. If the issue cannot be resolved by our remote support team, the robot is removed from the system until a certified technician fixes it on-site. The entire system continues running without interruption, even while retrieving the faulty robot.
Shelving and Totes
-
How tall does the shelving go?
Brightpick can extend to 19 feet / 5.8 meters using our high-density Brightpick Giraffe robots.
-
What type of totes can I use with Brightpick?
Brightpick robots can handle most tote types with a smooth, grippable surface. They accommodate a maximum tote size of 600×400mm, with heights between 220 and 300mm required for robotic picking.
-
What's the maximum weight per tote?
50 lbs / 23 kg per tote.
-
Can you store multiple SKUs in one tote?
Yes. The storage totes can be split into a maximum of 2 sub-sections for robotic picking or 8 sub-sections for Goods-to-Person picking.
-
Can we use our existing warehouse shelving?
We can evaluate your existing shelving, but new racks are usually recommended to guarantee optimal robot performance.
Installation
-
How long does installation take?
On-site installation typically takes 3-4 weeks. From PO to installation it typically takes 4-7 months, depending on our current manufacturing backlog.
-
Who does the installation?
Brightpick has a dedicated installation team. We do not outsource installation to third parties.
-
Is Brightpick suitable for existing brownfield warehouses?
Brightpick can be installed in almost any warehouse, including existing facilities, pick modules, and areas with limited clear height. Our solution does not require any strict floor flatness, high‑voltage power, or safety restrictions.
-
What are the floor flatness requirements?
Floor flatness tolerances vary by rack height. For installations using shelving up to 3.5 m (11.5 ft) high, the floor must not deviate more than 10 mm per meter (7/16 in per 3 ft). For shelving above 3.5 m, the tolerance is 6 mm per meter (1/4 in per 3 ft).
-
Can Brightpick Autopicker be installed in existing mezzanines?
Yes. Brightpick robots can be installed in most existing mezzanines and pick modules. Each robot has a minimum clear height of 2.15 meters / 7 feet and weighs approximately 200 kg / 440 lbs, which is suitable for most mezzanines.
-
Can we continue using our existing conveyors?
Yes. Brightpick robots can be easily integrated with your existing conveyors to retrieve and deposit totes as needed.
-
How can I expand the solution post-installation?
Scaling the Brightpick solution is quick and straightforward: add shelving to increase storage capacity and deploy additional robots to boost throughput. With no need for safety fencing, conveyors, or fixed navigation markers, this can be done in days.
Software
-
What does Brightpick Intuition software do?
Brightpick Intuition is our AI software that acts as the digital brain of your warehouse. Intuition creates a real-time digital twin of your operation, enabling our robots to see, think, and act with superhuman intelligence and human-like adaptability. The advanced software orchestrates our entire robot fleet with precision, controlling every movement and fulfillment workflow across your warehouse.
Intuition also tracks the exact location, quantity, and batch of every SKU – giving you a live, accurate view of your inventory and the ability to instantly recall or cycle-count any item when needed.
-
Can we use our existing WMS or ERP software with Brightpick?
Yes. Brightpick uses standard interfaces (APIs) to integrate seamlessly with your WMS / ERP. Our software receives new inventory and order data from your system and takes care of everything else, including fulfillment workflows and inventory tracking.
-
What is the uptime of the solution?
Brightpick installations consistently deliver over 99.5% uptime. With no single point of failure and interchangeable hardware, maintenance can be performed without halting operations – ensuring stable, reliable performance and minimal risk of unexpected downtime.
-
Does Brightpick offer performance dashboards?
We offer intuitive dashboards that give you full visibility into your operation, including system performance, order status, and inventory in real time. Our software also provides actionable insights such as low-inventory alerts and available storage and order buffer capacity.
-
Does Brightpick Intuition log all activity in case of failure?
Yes. All activity, including failures, is logged and traceable.
-
Does Brightpick do dynamic tote slotting?
Yes. Brightpick robots dynamically slot each tote into the most optimal storage location based on each SKU’s historical or expected picking frequency. The robots do this mainly overnight, but also throughout the day during quieter periods.
-
Where is the software hosted?
Brightpick installations include an on-premises server to host the software, eliminating connectivity risks.
-
How is the software updated?
The on-site server is updated remotely.
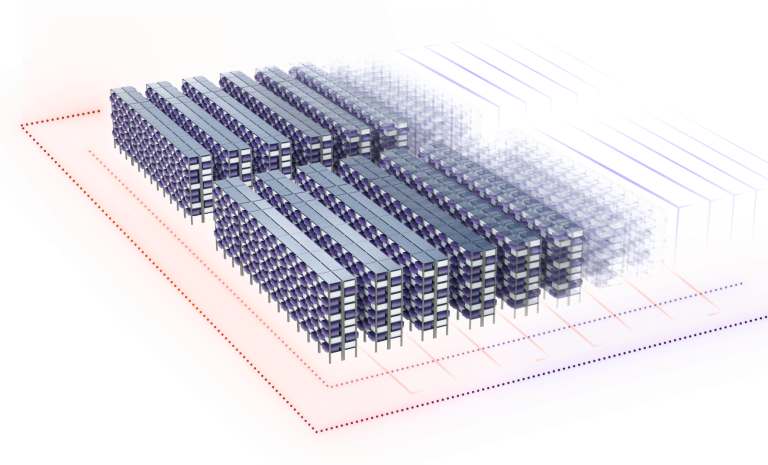