How Brightpick compares to Autostore
Cube storage systems like Autostore are known for their high storage density and reliability. But automation needs can differ wildly, and no single solution fits all. This month, we’re breaking down how Brightpick and cube storage stack up in real-world scenarios, and when one might have the edge over the other.
Degree of automation
Many automated storage and retrieval systems, including Autostore, focus solely on storing and retrieving items. Additional fulfillment tasks, such as post-pick order consolidation, buffering, or staging, often require separate systems. Brightpick tackles these tasks within one unified platform so companies can automate more of their process with fewer moving parts.
“While we had already installed a cube solution for storage and picking, we needed Brightpick to automate our post-pick order consolidation, buffer and dispatch,” said Ales Malucha, Chief Automation Office at Rohlik Group.
Robotic picking is another key difference. In cube systems, it’s possible to swap a human picker for a robot at a G2P station. However, no matter how good a robot is, inevitably there will be certain items it can’t pick (e.g. because of odd angles or damaged packaging). The key question is, what happens in these edge cases? Cube storage solutions require manual resets or routing those picks to a manual G2P station, adding extra steps like consolidation. By contrast, Brightpick Autopickers pick items directly in the aisle and, if needed, automatically deliver both the storage and order tote to a G2P station for manual completion in one streamlined process.
Storage density
Autostore excels at packing inventory, achieving the highest density per square foot. Brightpick also supports dense layouts with our 20-foot tall Giraffe robot, though our aisle-based design means we sacrifice some storage density. If density is your only priority, cube storage might be the way to go. But for most businesses, storage density is only one of several factors to consider in automation.
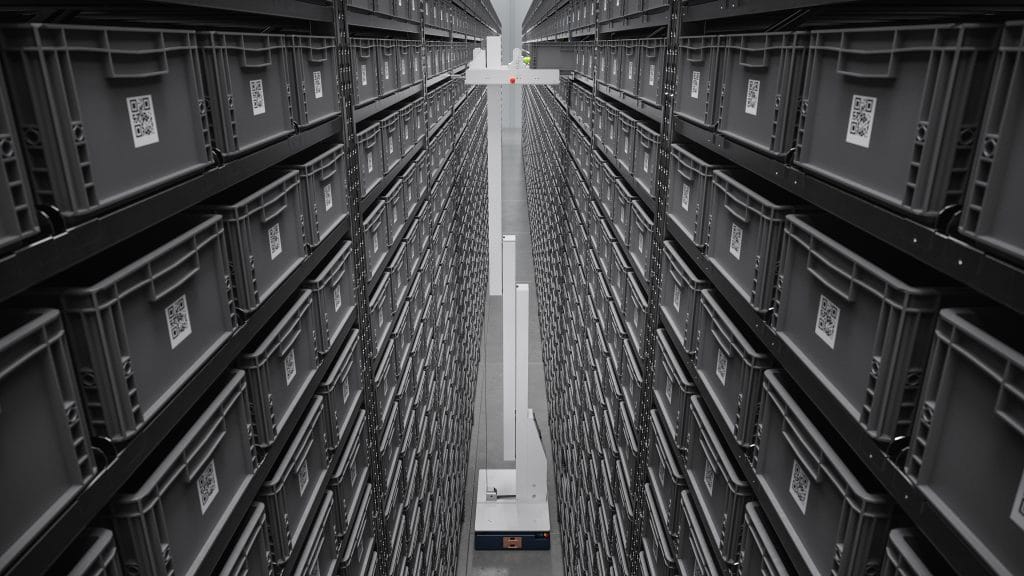
Operational flexibility
Autostore works best for slow-moving items. Because fast-moving items get picked so often, it doesn’t make sense to store them inside the system because you would need to replenish them almost as fast as you’d be picking them out. That’s why typically you see a manual pallet storage area for these fast-movers next to a cube system.
Brightpick manages both fast and slow items through our Fast Lane assisted picking feature. Robots pull up to designated spots where humans pick directly from pallets or cases into our robots, eliminating the need to decant fast-moving products entirely.
In addition, cube systems may struggle with throughput when SKU distribution is flat, as items get buried in stacks and robots have to dig for them, which significantly increases cycle times. By contrast, Brightpick’s aisle-based design means we have access to all inventory at all times.
“We have a very flat product curve. We pick most of our SKUs at least once per two days, so we needed a more dynamic solution that would let us direct picking operations to any one product at any one time,” said Matt Johnson, CEO of The Feed. “With a cube solution, if a product is buried at the bottom of a stack, that order risks getting held up. Brightpick quickly stood out as the only solution that had the capabilities we needed – it was the perfect combination of density, speed and cost.”
Installation
Autostore demand perfectly flat floors, long lead times, and can be expensive to expand or relocate. It also often requires additional infrastructure such as conveyors.
Brightpick robots can be deployed in weeks in most existing facilities, require minimal retrofitting, do not need conveyors or special safety fencing, and can be easily relocated to a different warehouse.
“We looked at a number of automation options, starting with cube solutions like those used by our competitors. Throughout the process, we realized that Brightpick was even better for us because it offered a more flexible and cost-effective solution,” said Tomas Cervenka, CEO of MTBIKER. “It fit better with our processes, didn’t require any conveyor belts and provided excellent software integration.”
Maintenance and reliability
Maintaining cube systems may require pausing the entire grid, for example if a technician needs to access a robot that is stuck, which creates a single point of failure.
With Brightpick, technicians can work safely without stopping the system. Even if some robots are offline, the remaining fleet keeps running, and built-in spare capacity helps maintain performance, resulting in practically 100% uptime.
Choosing the right fit
No single automation solution suits every operation. Autostore can be a good fit when storage density is the top priority and SKUs follow a classic volume distribution. Brightpick, on the other hand, offers greater automation, more operational flexibility, and simpler installation and maintenance. Understanding your priorities will help you choose the best fit for your needs.
Ready to embrace the future of AI? Brightpick offers an easy path to fully automate your order fulfillment.
Get started with Brightpick