Pros and cons of different robotics solutions for order fulfillment
How to choose the right picking automation for your warehouse
Labor for order picking can account for up to 50% of total warehouse costs. To remain competitive and deliver exceptional customer service, warehouse operators must overcome two industry-wide challenges: persistent labor shortages and high picking error rates.
Finding and retaining qualified labor has been the #1 challenge for warehouse operators since 2017. Meanwhile, 62% of retailers cite manual processes and human errors as the number one root cause for inventory and fulfillment issues.
To combat these challenges and reduce costs, companies are increasingly introducing robots into their warehouses. Automation improves picking accuracy, reduces labor needs and lowers fulfillment costs.
There is no one-size-fits-all solution when it comes to warehouse automation and each system has its own pros and cons. Let’s take a look at how the most common automated fulfillment systems compare to each other.
Shuttle Systems
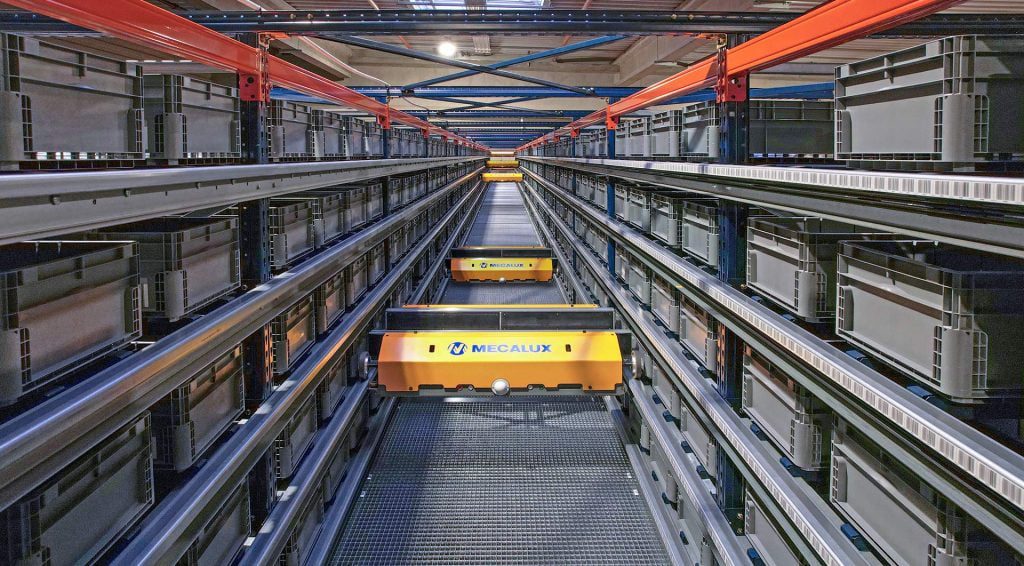
In shuttle systems, small robots called shuttles travel through aisles on rails, retrieve totes from storage and bring them to a lift. The lift takes the totes down to a conveyor, which then transports them to picking stations. After all the items for the order are picked, the totes are returned to storage.
Pros:
- High throughput: shuttles travel at high speeds and can typically access each tote directly from the aisle, which results in a high throughput.
- High density: shuttle systems can reach heights of up to 60 feet, which makes them space efficient for large warehouses with lots of vertical space.
- Long track record: these systems have been on the market for 20+ years, with lots of established vendors able to supply and service them.
Cons:
- High costs: shuttle systems require significant capital investment to pay for engineered racking, conveyors and lifts. The cost of a shuttle system typically exceeds $5-10 million. In addition, the complex machinery is costly to maintain and each installation requires extensive spare parts inventory to minimize downtime in case of failure.
- Long installation times: it typically takes 1-2 years to install a shuttle system given the extensive infrastructure required and long lead times from suppliers.
- No flexibility: shuttle systems cannot be easily reconfigured or scaled up given the extensive infrastructure required.
- Single points of failure: a broken lift or conveyor belt can cause the whole system to stop for an extended period of time.
Cube storage
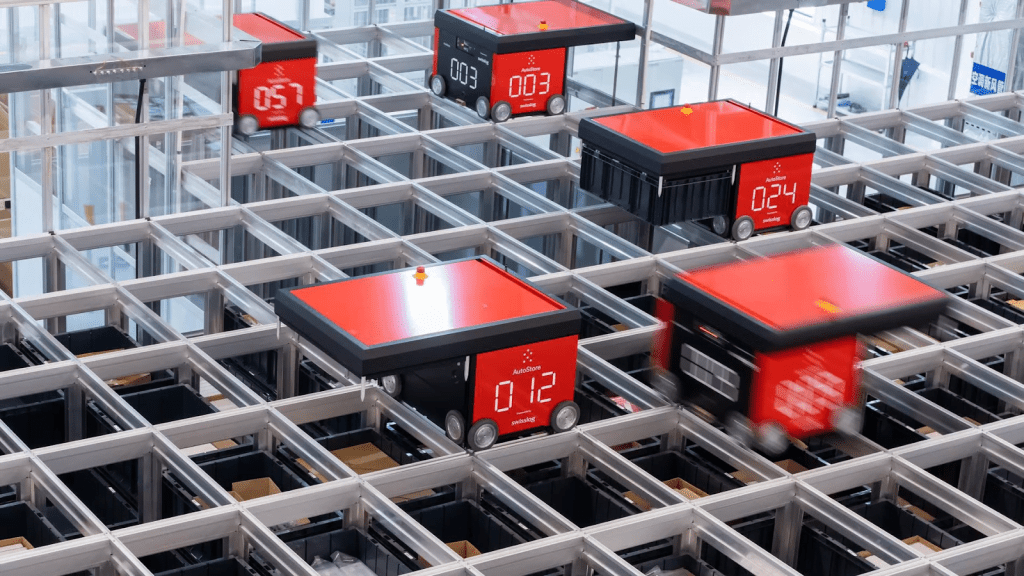
Cube storage consists of totes stacked on top of each other in a cube-like structure. Robots travel on top of the grid, retrieve totes from inside the cube and deliver them to external picking stations. After all the items for the order are picked, the robots return the totes back into the cube.
Pros:
- Density: cube storage offers high density because it eliminates the need for aisles and can reach heights of up to 20 feet / 6 meters.
- High throughput (for items stored at the top of the cube): the robots travel the grid at high speeds, which results in high throughput for items stored near the top of the grid where they are easily accessible.
- No single point of failure: each robot operates independently and one breaking down does not affect the others.
Cons:
- High upfront costs: cube systems require high upfront capital investment to build the grid and supporting infrastructure. They also typically require special totes.
- Limited flexibility: while cube storage is more modular than shuttle, it still requires a fixed structure that cannot be easily reconfigured, moved or expanded. In addition, cube storage has strict floor flatness requirements which may require additional investment in the warehouse, especially for brownfield facilities.
- Low throughput (for items stored at the bottom of the cube): to access totes at the bottom of the cube, the robots first need to “dig” out the totes above them, which slows down the retrieval process and throughput.
Goods-to-Person (G2P) AMRs
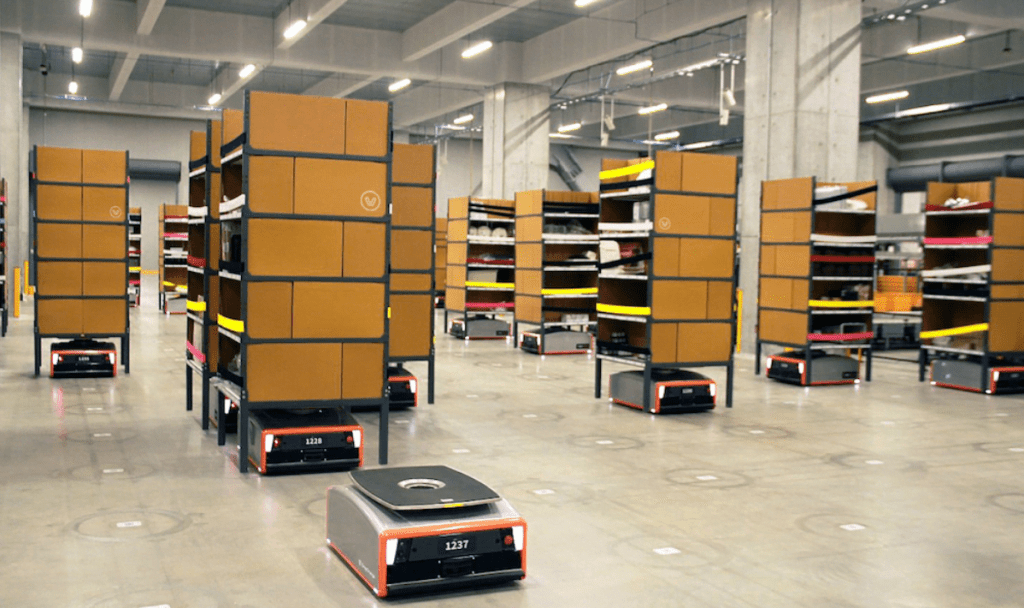
Goods-to-Person systems use autonomous mobile robots (AMRs) to retrieve totes or racks from storage and transport them to centralized picking stations. After all the items for the order are picked, the AMRs return the remaining items back into storage.
Pros:
- Flexibility: Goods-to-Person AMRs do not require heavy fixed infrastructure such as conveyors or engineered racking, which makes them relatively easy to implement and scale.
- Lower upfront cost: AMRs typically cost less to implement and maintain than shuttle or cube storage, primarily because they do not need much supporting infrastructure.
- No single point of failure: each robot operates independently and one breaking down does not affect the others.
- Density: Some G2P AMRs can reach heights of up to 30 feet or 10 meters, which results in high storage density.
Cons:
- Low throughput: Goods-to-Person AMRs typically deliver lower throughput due to the robots’ slower speeds (compared to shuttle or cube robots). While adding more robots can increase throughput, adding too many robots can also result in congestion and inefficiency.
- Navigation: G2P AMRs typically use fixed guidance systems on the floor (such as QR codes) to move around the warehouse, which adds maintenance complexity and cost.
- Safety: G2P AMRs are typically not safe around humans given their heavy loads, which means the automation area needs to be fenced off.
Directed Picking AMRs
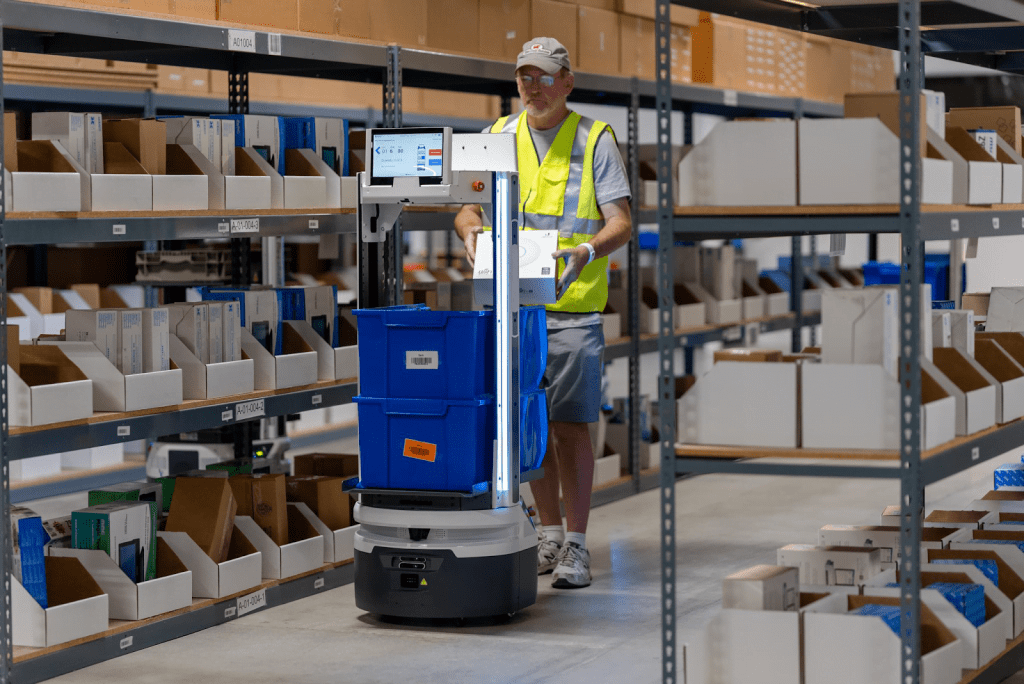
In directed picking, humans remove items directly from pallets or storage shelves and place them onto autonomous mobile robots. The AMRs move around the warehouse from one pick location to the next until the order is fully picked. This reduces travel distances for human pickers and increases their productivity.
Pros:
- Flexibility: directed picking AMRs do not require any changes to the warehouse since humans continue picking directly from pallets or storage shelves (unlike other automated fulfillment systems which use totes for storage). This means directed picking robots are simple to install and can be easily reconfigured in case of changes to the warehouse.
- Low cost: directed picking AMRs typically cost less than other forms of automation. They do not need totes or specialty shelving. In addition, they require fewer robots because they move from one pick location directly to the next, instead of having to go back and forth to picking stations like Goods-to-Person systems.
- No single point of failure: each robot operates independently and one breaking down does not affect the others.
Cons:
- Low labor and cost savings: directed picking solutions deliver lower labor savings than Goods-to-Person systems because they still require human pickers to walk in between picks. Human pickers in directed picking systems typically achieve 100-180 picks per hour compared to 300+ in Goods-to-Person stations.
- Does not automate replenishment: unlike other automated fulfillment systems, directed picking AMRs do not automate putaway and still require humans to replenish storage.
- No improvement in density: directed picking systems do not increase density compared to manual picking. Human pickers still need to operate inside the storage area and pick directly from the shelves, which limits how high the shelves and how narrow the aisles can be.
Autonomous Mobile Picking Robots
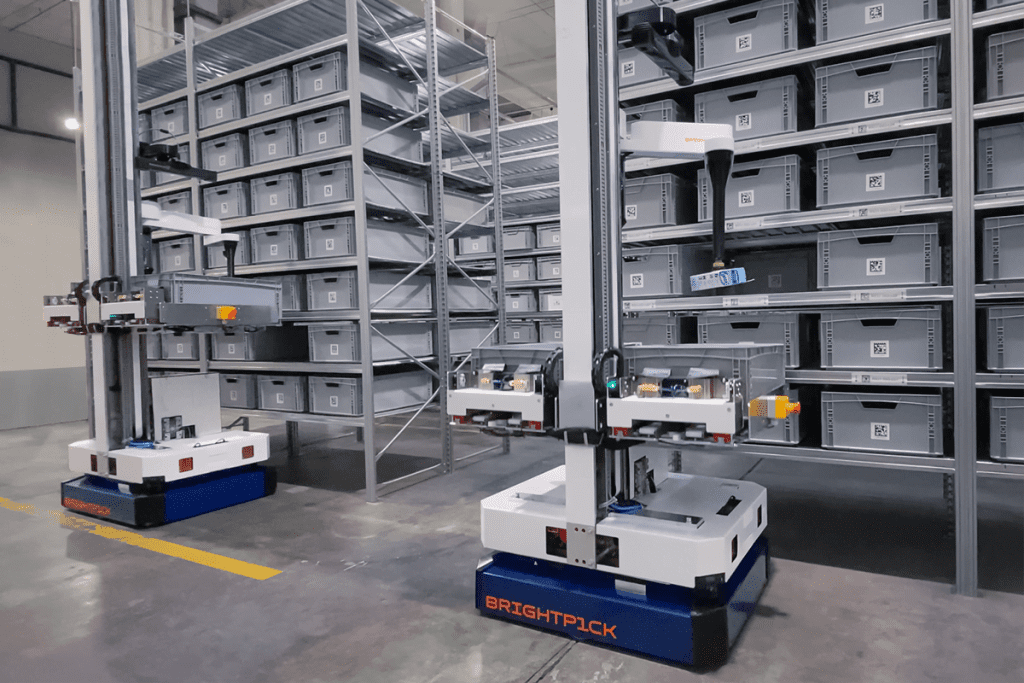
Autonomous mobile picking robots can robotically pick and consolidate orders directly in the warehouse aisles. Much like a human with a cart, these robots move around the warehouse and consolidate orders by picking items directly.
The robots use a two-tote design to retrieve storage totes from shelving and robotically pick individual items from those storage totes into an adjacent order tote. They do this repeatedly as they moves through the warehouse aisles until the order or batch has been fully picked.
Pros:
- High throughput: Unlike shuttle, cube storage or G2P AMRs, these robots do not need to travel back and forth to centralized picking stations for each pick, which results in faster picking and higher throughput.
- Maximum labor savings: autonomous mobile picking robots deliver maximum labor savings thanks to their robotic picking capabilities.
- Flexibility: these robots work with standard shelving and totes and do not require fencing or heavy fixed infrastructure such as conveyors. This makes them easy to implement and scale.
- No single point of failure: each robot operates independently and one breaking down does not affect the others.
Cons:
- Limitations of robotic picking: most warehouses will have some items that cannot be robotically picked. That is why these robots also have integrated Goods-to-Person capabilities for items that require human picking.
- Few vendors: autonomous mobile picking is a novel technology and there is currently only one vendor offering this technology (Brightpick).
Each type of automation has its pros and cons depending on your needs. If you’re interested in learning more about how efficient each system is based on how much labor and how many robots it requires, you can download our White Paper: How to Maximize Efficiency of Order Picking With Autonomous Mobile Picking
About Brightpick
Brightpick is a leader in AI-powered robotic solutions for warehouses. The company’s multi-purpose AI robots enable warehouses of any size to fully automate order picking, buffering, consolidation, dispatch, and stock replenishment. The award-winning Brightpick solution takes just weeks to deploy and allows companies to keep their fulfillment labor to a minimum. With offices in the US and Europe, Brightpick has more than 250 employees and hundreds of AI robots deployed with customers.
Get started with Brightpick